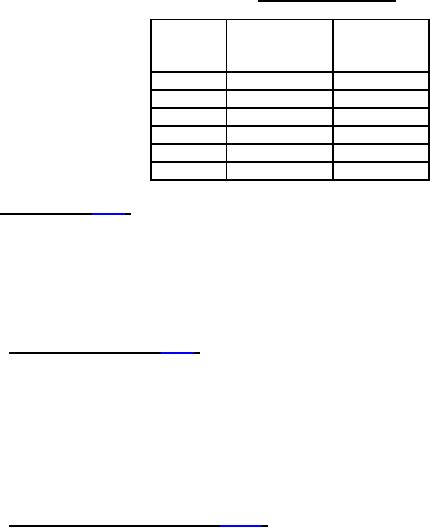
MIL-DTL-5593E
TABLE VI. Flexibility test weight.
Flexibility
Flexibility
Dash
test weight
test weight
number
Max pounds
Max kg
2
.25
0.11
3
.25
0.11
4
.25
0.11
6
.56
0.25
8
1.00
0.45
10
2.00
0.91
4.6.9 Kinking (see 3.4.8). Hose when subjected to the kinking test shall meet the requirements of
3.4.8. The following details shall apply:
a. A length of hose shall be bent around a mandrel, having a diameter conforming to the kinking test
b. The hose shall be exposed to a temperature of 158°F ±2°F (70°C ± 1.11°C) for 3 hours.
c. At the end of the 3-hour period, the hose shall meet the requirements specified in 3.4.8.
4.6.10 Vacuum collapse (see 3.4.9). Hose when subjected to the vacuum collapse test shall meet the
requirements of 3.4.9. The following details shall apply:
a. A length of hose shall be bent around a mandrel having a diameter of 10 times the outside
diameter of the hose.
b. A vacuum of 20 inches of mercury (50.8 centimeters of mercury) shall be applied to hose with an
inside diameter of less than .500 inch (12.70 mm).
c. A vacuum of 10 inches of mercury (25.4 centimeters of mercury) shall be applied to hose with an
inside diameter of .500 inch (12.70 mm) and larger.
4.6.11 Low temperature flexibility (see 3.4.10). Hoses when subjected to the low temperature
flexibility test shall meet the requirements of 3.4.10. The following details shall apply:
a. Two sample hoses, each 12 inches (30.5 cm) long, are required for this test. One hose shall be
oil aged and one hose shall be air aged.
(1) The sample to be oil-aged shall be filled with fluid or immersed in fluid in accordance with
MIL-PRF-5606, MIL-PRF-87257, or MIL-PRF-83282.
(2) The sample to be air aged shall be open to the oven atmosphere in step b.
b. Both samples shall be conditioned in an oven at a temperature of 158°F ±2°F (70°C ±1.11°C) for a
minimum of 168 continuous hours.
c. After conditioning, both samples shall be placed in a cold chamber at -65°F ±2°F (-53.89°C
±1.11°C) for 72 hours.
d. After this time and while at -65°F ±2°F (-53.89°C ±1.11°C), the test samples shall be flexed
through 180° over a mandrel of the same temperature having a diameter of 10 times the outside
diameter of the hose for 1 cycle.
e. The rate of cycling is 1 cycle in 4 seconds.
f. The samples shall then be subjected to the proof pressure test (see 4.6.2).
14
For Parts Inquires call Parts Hangar, Inc (727) 493-0744
© Copyright 2015 Integrated Publishing, Inc.
A Service Disabled Veteran Owned Small Business