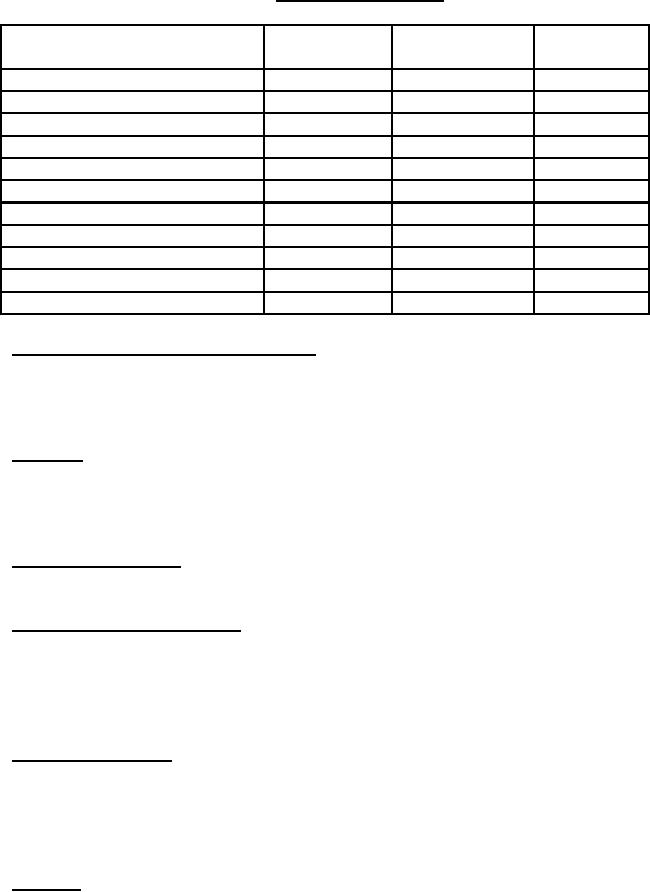
MIL-PRF-28523C
TABLE II. Test method references.
Requirement
ASTM Test
Reference
paragraph
Method Standard
paragraph
Hose size (inside diameter)
3.7
ASTM D 380
Hose length
3.7
ASTM D 380
Tube and cover thickness
3.2.1 and 3.2.3
ASTM D 380
Proof pressure
3.5 and table I
ASTM D 380
4.7.1
Burst pressure
3.5 and table I
ASTM D 380
4.7.2
Tensile strength and elongation
3.5 and table I
ASTM D 412
4.7.3
Swelling
3.5.1.1
ASTM D 471
4.7.4
Accelerated aging
3.5.3
ASTM D 573
4.7.5
Adhesion
3.5 and table I
ASTM D 413
4.7.6
Oil immersion
3.5.2
ASTM D 471
4.7.7
Ozone
3.5.4
ASTM D 1149
4.7.8
4.7.1 Hydrostatic proof test, coupled assemblies. Samples selected after couplings have been
reattached shall be subjected to the hydrostatic proof test pressure specified in table I in
accordance with ASTM D 380. Water shall be used as the test media. Leakage or other evidence
of defects shall be cause for rejection.
4.7.2 Burst test. Hose samples selected shall be subjected to the hydrostatic straight bursting test
of ASTM D 380. Water shall be used as the test media. Any suitable coupling other than those
specified in 3.4 may be used for this test. Failure of the hose at a pressure below the minimum
burst pressure specified in table I shall be cause for rejection of the lot.
4.7.3 Initial tensile properties. Initial tensile strength and ultimate elongation shall be determined
by the procedure given in ASTM D 412, using specimens cut with die C of ASTM D 412.
4.7.4 Volume change after immersion. The change in volume of samples of the tube, after
immersion for 22 ± 0.25 hours at a temperature of 73 ± 4 degrees Fahrenheit (°F)
(23 ± 2 degrees Celsius (°C)) in type IV reagent water of ASTM D 1193 shall be determined in
accordance with ASTM D 471. The change in volume shall be reported as a percent of the
original volume.
4.7.5 Accelerated aging test. Hose samples selected shall be subjected to accelerated aging in
accordance with ASTM D 573, except that the time of aging shall be 70 ± 0.50 hours at
212 ± 4 °F (100 ± 2 °C). After aging, the tensile strength shall be not less than 80 percent of the
values specified in table I, and the ultimate elongation shall be not less than 50 percent of the
values specified in table I. The die for cutting the specimen shall be C of ASTM D 412.
4.7.6 Adhesion. For hose assemblies selected, prepare ring specimens as described in ASTM D
380. The adhesion shall be determined in accordance with the machine method of ASTM D 473.
6
For Parts Inquires call Parts Hangar, Inc (727) 493-0744
© Copyright 2015 Integrated Publishing, Inc.
A Service Disabled Veteran Owned Small Business